Reducing emissions while increasing refinery margin
A chemical heat pump that absorbs energy inside industrial waste heat has the potential to reduce pressure on refinery margin by fluctuating gas, electricity, and CO2 costs
Author: Bernd Van Den Bossche
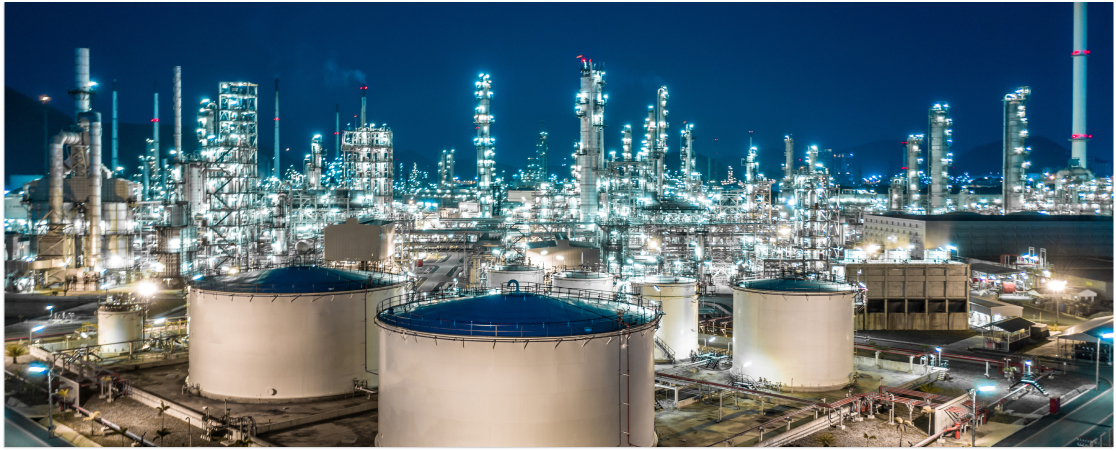
Table of Contents
- Increasing margin per barrel
- Turning cooling load into CO₂-neutral, Opex-free steam
- Commercial-scale references
- Refinery applications
- FCC unit
- Diesel hydrotreater
- Delayed coker unit
- Conclusion
European refiners are facing a significant challenge in balancing the so-called energy trilemma in providing affordable, reliable, and clean energy. Prioritising investments in energy efficiency, such as the true decarbonisation of steam supply, allows for increased future refinery margins. Against this backdrop, the proprietary Qpinch Heat Transformer (QHT) has demonstrated refinery-scale, CO₂-neutral, and quasi-Opex-free process steam, hedging the pressure on operating margin by fluctuating gas, electricity, and CO₂ costs.
Increasing margin per barrel
Following the 2015 Paris Agreement, increased societal expectations have moved most oil and gas corporates to pledge ambitions towards a future with net-zero greenhouse gas (GHG) emissions.1 The challenge of converting the ambitions into a set of executable projects comes on top of the two other main challenges the industry is facing: to supply secure and affordable energy to meet society’s increasing energy needs. All of this is in a background where global peak demand for oil products is right ahead of us or already behind us, depending on the exact forecast.2
The uncertain macroeconomic outlook makes it difficult to prioritise investments. One option is to develop projects that increase the cash margin per barrel without compromising on resilience to future demand fluctuations and reducing CO₂ emissions in parallel. A textbook example of such investment is energy efficiency. Particularly for European refiners, where energy cost is putting an ever-increasing pressure on margins, energy efficiency improvements can make a difference and prevent rationalisation.³
It is estimated that the Scope 1 and 2 emissions of oil refineries represent about 4% of global CO₂ emissions.4 Most emissions are coming from fuel combustion in furnaces, heaters, and steam boilers. Boilers contribute 20-50% of a refinery’s total CO₂ emissions.5 The exactvalue of a particular refinery is heavily influenced by its fuelmix used for steam generation, the level of heat integration,the refinery’s complexity, and the overall efficiency of itssteam system.
Regarding fuel mix, the higher the C/H ratio in the fuel, the more CO₂ is emitted per unit of combustion heat. So, a refinery power plant running on fuel gas or natural gas will have lower CO₂ emissions than one running on heavy fuel oil or even vacuum residue. The efficiency of a boiler is mostly linked to the construction year, with more recent burners and boiler arrangements possessing higher conversion efficiencies, thus fewer CO₂ molecules emitted per unit of steam production. Steam header losses can be minimised by insulation and proper steam trap maintenance.
The more complex a refinery and the more integrated with downstream petrochemical process units, the more value is generated per barrel of crude intake, but the higher the absolute CO₂ emissions. The reason is that each conversion step has a certain heat requirement to overcome thermodynamical barriers. On the other hand, integrated and more complex refineries have more opportunities for heat integration to increase overall energy efficiency and decrease GHG intensity per ton of product generated.
The more complex a refinery and the more integrated with downstream petrochemical process units, the more value is generated per barrel of crude intake, but the higher the absolute CO₂ emissions
Furthermore, an intensity of 30 kg CO₂-equivalent emissions per barrel refinery output has been estimated for European refiners, with top and worst performers at ±50% of this value.⁶ Taking into account a near future without free allowances and with a European Union Emission Trading Scheme (ETS) price of €100/t CO₂, this means an additional burden on the refinery margin of €3 per barrel on average, coming on top of the already reduced margin due to high energy cost. So, there is a significant investment opportunity in acquiring CO₂-neutral steam through energy efficiency.
But what exactly would be the win of a ton of steam? The value of saving a ton of steam would be the marginal cost of steam (the value of the most expensive ton of steam the refinery is consuming at a moment in time). In most cases in Europe, this will be a ton of steam coming from a steam boiler, fed with grid natural gas and without free allowance on the CO₂ emission.
Figure 1 Process sketch of the QHT
Assuming 90% energy conversion in the burner, 0.2 tons CO₂ emission per MWh natural gas and boiler feed water available at 100°C, then one ton of steam represents a value of approximately €50. This value assumes a natural gas cost of €50/MWh and €100/ton CO₂ EU ETS and is neglecting header losses or the cost of boiler feed water. Translated to an average European refiner with 20% of emissions linked to steam generation and 30 kg emissions per barrel of refined product, the potential goes up to €2/ barrel increase in margin. This represents significant leverage against other margin pressure factors.
Turning cooling load into CO₂-neutral, Opex-free steam
The ATP-ADP cycle is an energy distribution system that fuels all living cells on Earth. Adenosine triphosphate (ATP) and its derivative adenosine diphosphate (ADP) are used as an energy carrier to transport energy on a cellular scale. ADP, the base molecule, gets charged with an extra phosphate group and turns into ATP in areas with excess energy. In contrast, the reverse reaction releases energy in energy-poor areas. The liquid ATP and ADP are easily transported throughout the cellular fluids.
The Qpinch Heat Transformer (QHT) is an absorption heat pump which uses phosphoric acid (PA) as working medium. Under right conditions, PA forms oligomers and thus absorbs residual energy available in industrial waste heat. The reversible reaction is used to release the absorbed energy at a higher temperature so it can be reused as process heat. Useful examples of industrial waste heat are hot liquids, condensing column overheads, and excess steam that currently are condensed/cooled using air fans and cooling water exchangers. Examples of useful process heat are steam, thermal oil, and hot water.
A QHT unit consists of two heat exchangers with a closed loop of PA between them (see Figure 1). The cold reactor absorbs industrial waste heat at low temperature, whereas the hot reactor releases new process heat at high temperature. However, in both reactors, heat is transferred indirectly towards the service side, so the internal PA never encounters the waste heat source or process heat sink, respectively. Furthermore, the PA is food-grade. The
system being a closed loop and PA an inorganic chemical, there is no degradation, consumption, or emission of chemicals. The PA has no other hazardous effect than its acid-linked corrosivity. So the QHT unit does not represent any flammability, toxicity, or explosion risk and, thus, does not need any flare connection.
Figure 2 Single step temperature lifts achievable with the QHT
Figure 2 illustrates the operational range and temperature lift a QHT can generate. As a rule of thumb, waste heat at 80°C can be converted to useful heat at 120°C, while waste heat at 120°C can be lifted to a maximum of 210°C.
The QHT converts about half the waste heat duty into new process heat, while the other half is released at ambient temperature as the driving force for the chemical reaction, hence preventing the need for electricity. On a commercial scale, this split does not jeopardise the attractivity because, without Qpinch, the complete waste heat duty would be released to ambient temperature, creating even additional costs to cool down the waste heat. Maybe the most attractive characteristic of a PA-based heat transformer is the fact that all products remain in the liquid state, so only a marginal amount of electricity (centrifugal pumps) is required to operate the QHT in a safe and reliable way.
Indeed, it takes ±300 kW of electricity to generate 10 MW of new process heat, while conventional heat pump technology would require at least eight times more electricity. Moreover, the electricity-to-heat ratio of a QHT is not affected by the temperature lift between the low-temperature waste heat source and the high-temperature sink. As such, this augmented economical coefficient of performance (eCOP: ratio of electricity input per unit of high-temperature output) is a unique driver for the financial attractivity of the QHT technology.
It is assumed that in the near future in Europe, the marginal cost of electricity will be driven by both renewable supplies (wind, PV) and gas turbines. The latter is a flexibility measure towards fluctuating electricity demand, a parameter more difficult to meet with, for example, nuclear energy. Assuming so, the price of electricity will still be affected by natural gas and CO₂ pricing. For truly net zero Scope 1 and Scope 2 emissions, it is key to minimise dependency on commodities with
variable pricing and CO₂ credits or taxes. Figure 3 displays the marginal steam cost for an industrial facility in Europe based on Dutch TTF natural gas prices and EU ETS prices.
The yellow curve gives the business-as-usual case where steam is produced by combustion of natural gas, and EU ETS credits are purchased to cover emissions. The blue and red curves display the steam cost when using a mechanical vapour re-compressor (MVR) and a QHT. The very low total operational cost of a QHT means a plant owner can hedge their steam price during the full lifecycle of the installation, being the industry standard of at least 20 years long.
Figure 3 Historical marginal steam cost for EU industrial consumer in EUR/ton steam for different methods of steam generation (MVR = mechanical vapour recompression)
Commercial-scale references
Pioneering references of the QHT technology are situated in the chemical industry (such as SABIC, Kuraray, and Borealis). Operational examples have confirmed the unique temperature lift and low electrical consumption, as previously explained. In addition, new significant features
appeared, such as the intrinsic flexibility of the chemistry to production fluctuations. One such example is shown in Figure 4, which displays the actual operating pressure of the customer’s steam header in red. In blue, one can see the mass flow of steam produced by the QHT and released into the header. At 9:35 pm on April 13th, the overall header pressure suddenly decreases from 4.1 to 3.5 bar due to an upset in demand by one big steam consumer. The QHT exports steam via a pressure control valve on the customer’s header and automatically increases exports from 800 to 1,350 kg/h to buffer the falling header pressure. When the header pressure was restored, the QHT unit automatically returned to nominal condition. The time span of the action was +/-25 minutes, and no operator involvement was needed to control the QHT behaviour.
Figure 4 Operational example of the QHT unit flexibly buffering the customer’s steam header in case of a calamity
Refinery applications
As a very flexible energy efficiency technology, applications
are not limited to the chemical industry. In refining, CO₂ emissions related to steam generation can be saved by valorising low-temperature heat sources in the vacuum unit, hydrocracker, FCC, hydrotreaters, and coker unit. This not only assures direct savings in energy costs but also indirect savings in cooling capacity and utility-related maintenance costs. Based on heat integration studies performed by Qpinch for European operators, a ballpark total available roll-out potential of 100 t/h CO₂-neutral quasi-Opex-free steam production was identified per 100,000 bbl/d refining capacity. This represents an absolute and annually recurrent CO₂ saving of 120,000 t/y for a rather small-scale European refinery. A detailed discussion of three different refinery units is provided in the following sections (FCC unit, diesel hydrotreater, and delayed coker unit).
FCC unit
The FCC is a very versatile unit in a refinery complex. It offers the possibility to produce high-quality fuels and olefins from heavy gasoil, atmospheric residues, and other high-boiling point feedstocks. The FCC unit also produces a vast amount of steam to drive other plant operations. However, several coolers inside the FCC are disposing of low-grade heat at a fairly high temperature (>80°C). Examples are the main fractionator overhead condenser, the light cycle oil (LCO) cooler, the heavy cycle oil (HCO) cooler, and the slurry cooler.
Qpinch has already investigated several applications of its QHT technology to turn these waste heat sources into Opex-free and CO₂-neutral low- and medium-pressure steam. Figure 5 shows a battery limit heat and mass balance of a QHT engineered for a European refinery where the condensation heat of the main fractionator overhead is lifted into 4.2 tons/hour of medium-pressure steam at 11 bar gauge. Note that only 85 kW of electrical power is required to drive the process unit.
Figure 5 Example of a QHT (white box) designed for a European refiner’s FCC unit combining absorbing the condensation heat from the main fractionator overhead and the excess LPS and lifting this heat into MPS (LPS = low-pressure steam)
Diesel hydrotreater
Hydrotreating can be performed on various streams with the aim of reducing the sulphur content: naphtha, diesel, and kerosene. The process is based on the use of a metal hydrogenation catalyst and occurs at elevated temperatures and pressures. Feed heaters are used to bring the feedstock to the correct operating temperature. Downstream of the reactor, a feed product heat exchanger is used to cool the product and preheat the feed. Nevertheless, conventional air fan cooling is still required to bring the temperature down to separator temperature. In the stripper section, light fractions are separated from the desulphurised product.
The overhead of this stripper and the diesel product are in the business-as-usual case, respectively condensed and cooled against air as well. The Qpinch chemical heat transformer can recover the energy in those streams and create useful low-pressure steam. One centralised QHT unit can cool down the three different waste heat sources inside an HDS unit. Qpinch has already engineered solutions for several European refiners for this process unit. Figure 6 shows the battery limit flows for such an example.
Figure 6 Example of a centralised QHT (white box) designed for a European refiner’s diesel hydrotreater unit combining residual heat from the stripper overhead, reactor effluent, and desulphurised product coolers (BFW = boiler feed water, LPS = low-pressure steam)
Delayed coker unit
A coker or delayed coker unit (DCU) is the most extreme step in turning residual bottom products into high-value refinery products. Several different technologies exist, but generally the bottom flow of the vacuum unit is further thermally cracked with steam and high-pressure water into coke on the one hand and lighter products on the other. The different non-solid products are separated in the coker main fractionator column. The different coolers and condensers present in the side cuts of this distillation column are valuable waste heat sources to apply the QHT technology. Concrete examples are the heavy coker gasoil cooler, light coker gasoil cooler, and the main fractionator overhead condenser, containing mostly heavy naphtha. As with the previous examples, all these sources can be combined into one QHT unit to benefit from economies of scale in generating Opex-free and CO₂-neutral steam for the refinery network (see Figure 7).
Figure 7 Example of a centralised QHT (white box) designed for a European refiner’s DCU combining residual heat from the main fractionator overhead and the light and heavy gasoil coolers (BFW = boiler feed water, LPS = low-pressure steam)
Conclusion
In an environment challenged by the energy trilemma, the QHT has the potential to bring certainty and reduce the pressure on refinery margin by fluctuating gas, electricity, and CO₂ costs. The patented chemical heat pump (QHT) is fully driven by the waste heat source, allowing COP >25 on a megawatt scale. The patented technology is applicable in a temperature range between 80°C and 210°C.
All figures/graphics shown in this article are property of Qpinch BV and cannot be used, reproduced or distributed without Qpinch BV’s written consent. Qpinch heat Transformer (QHT) is a mark of Qpinch BV.
References
1 Westervelt R, Race to Zero, Chemical Week by S&P Global, 184, No. 9, April 18, 2022.
2 McKinsey & Company, Global Energy Perspective 2022, published April 26, 2022 and retrieved in Feb 2023 via www.mckinsey.com/ industries/oil-and-gas/our-insights/global-energy-perspective-2022.
3 Ellerington T, Refining Competitiveness – Increasing the Pace, presented at European Refining Technology Conference, Nov 2022.
4 Lei T, Guan D, Shan Y, Zheng B, Liang X, Meng J, Tao S, Adaptive CO2 emissions mitigation strategies of global oil refineries in all age groups, One Earth, 4(8), 1114-1126, 2021.
5 Zhang Z, Borhani T N G, El-Naas M H, Carbon Capture in Exergetic, Energetic and Environmental Dimensions (I Dincer, C O Colpan and O Kizilkan Eds.), 997-1016, 2018, Academia Press.
6 Szarek G, Increasing Competitiveness through Decarbonization, presented at European Refining Technology Conference, Nov 2022.
