Open the fence
How to reduce CO2 emission? That’s your day-to-day challenge as operations manager in the heavy process industries.
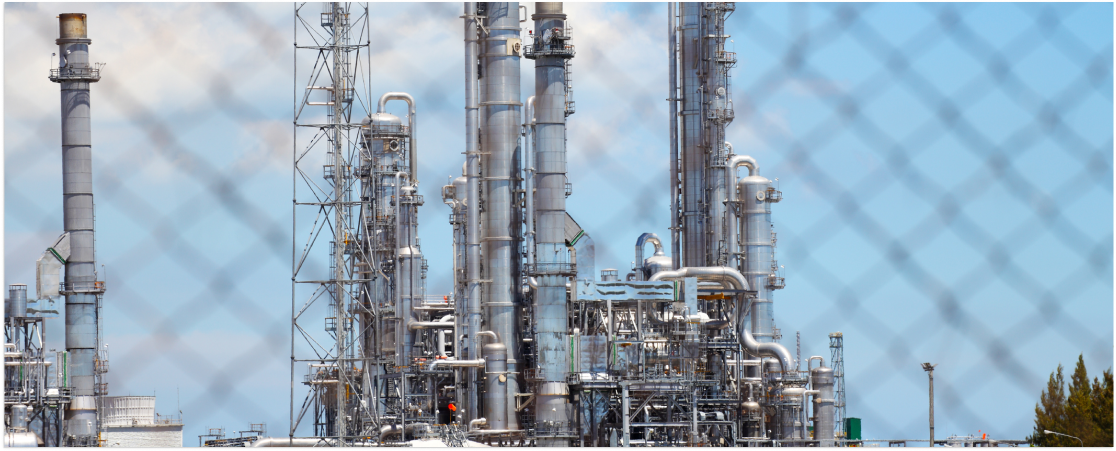
Table of Contents
- Non-invasive installation
How to reduce CO2 emission? That’s your day-to-day challenge as operations manager in the heavy process industries. Aside from ambitious financial and production targets, there are challenging safety and process continuity concerns to govern. Any policy adjustment in CO2 targets weighs gravely on the working reality of a production plant. Excellent planning is imperative and there can be some understandable opposition to short term introductions of new technology. Meet our now-tech that proves alert to all operational complexities and boasts a non-invasive implementation track that alleviates woes and worries. Helping ops managers open the fence and propel results forward, with confidence!
Experience is golden. At Qpinch, we are acolytes of that aphorism. That is why we focused our QHT (Qpinch Heat Transformer) tech on some of the real-life challenges operations managers face. We’ve taken ample amounts of deep R&D time (14 years, starting in 2008) to model and fine-tune a solution that aims at considerably raising process energy efficiency. Immediate and powerful gains can be made in crafty waste heat recovery. Instead of expelling refuse steam into the environment, we’re boosting it back to process heat, without using any electricity. An affluent resource that is already on premise.
Non-invasive installation
Operational disruptions can manifest in two main areas: production continuity and plant safety. So these get some special attention in our deployment. Of course, there’s no such thing as a non-invasive installation. But we have designed an agile system that minimises additional plant downtime. Our R&D surveys reveal this to be the acceptable threshold for operations professionals: an installation sufficiently light and unobtrusive so it can be fitted into your existing procedures and maintenance schedules.
We know we are talking to real-life experts. Rolled up sleeves kind of managers. So let’s talk about what’s so non-invasive:
- Proven tech: This is no immature field testing, nor a whimsical launch. We’ve adopted and respected every inch of groundwork a large scale industry solution requires. With 14 years of R&D, our QHT is tried and tested and ready to outperform the rest.
- Outside the fence: The larger part of construction can be performed outside the fence, drastically reducing any safety measures you need to organise. Proper add-on technology can be wheeled in and connected swiftly.
- Low-maintenance: A designed lack of complexity implies a low-maintenance cost & effort of the QHT installation. The system consists largely of standard and easily sourceable components. Making any repairs and upkeep pretty straightforward.
- Small plot size: The QHT installation offers great yield per surface. Its small dimensions and modular set-up make it combinable with other new tech or existing process infrastructure, optimising your plot allocation.
- Low-hindrance: The QHT device produces no disruptive vibrations or excessive noise inconvenience, as is the case with other technologies that require the use of turbo-compressors. The subsequent lower environmental permit requirements are an added bonus.
- Low energy requirements: The start-up and running of the QHT units require limited electricity (40 kW per MW steam output) and handle power fluctuations easily.
- Low cost: The cost of the various systems that cater CO2 reduction targets by means of energy efficiency can be quite disparate. The QHT system is distinctly cheaper than competing options.
- Now-tech reduces future investments: Implementing now-tech in the short term, can considerably reduce the amount of investments you will need to roll out in the long term. The larger, long term systems (Energy Substitution and Carbon Capturing & Storage tech) represent far greater process invasions. Now-tech can help to minimise the future requirements in other areas. Or the other way around: by not investing now, you will increase your future investment requirements and lose a competitive advantage.
